So that you do not build from capital structures, you cannot do without floor slabs. They will be needed in any case, regardless of the number of storeys of the house or garage, as well as their size.
Floor slabs are different. To figure out what kind of specific variety is required in your case, you can only familiarize yourself with their assortment and quality characteristics.
Reinforced concrete floor, what is it?
If you look at the definition, it becomes clear that a floor slab is a structural element of a building or other building object that divides it into separate floors. Their task is, together with other supporting structures, to provide the structure with structural rigidity. The slabs are rectangular in shape and are made mainly of reinforced concrete.
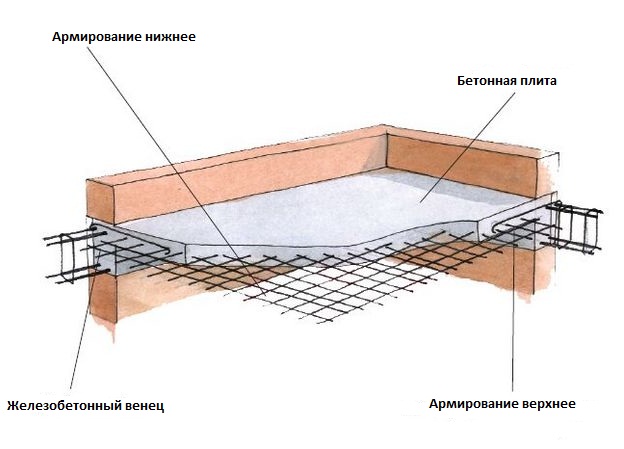
Scheme of reinforced concrete floor
Types of floor slabs
These building structures are distinguished by several parameters. According to the method of production, they are:
1. Monolithic.
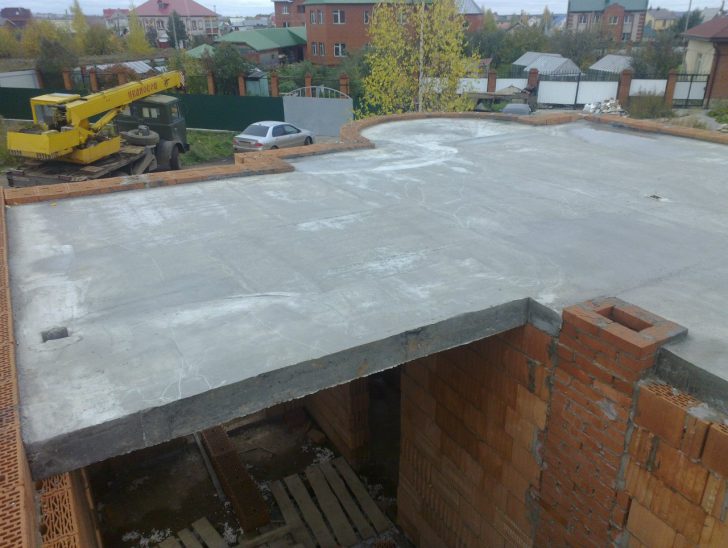
Monolithic floor slab
2. Precast concrete.
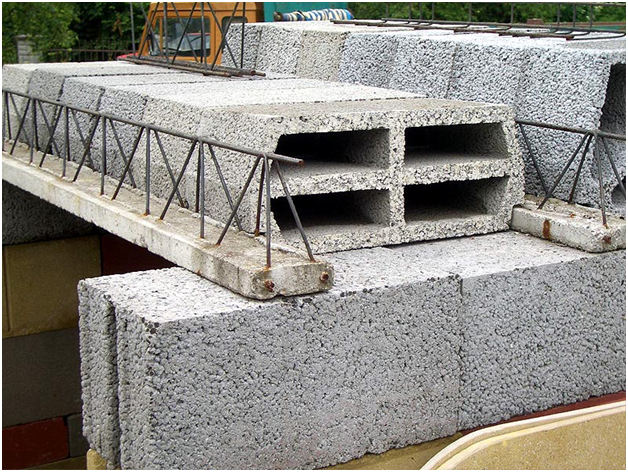
Prefabricated monolithic floor slab
The first are made directly on the construction site. The process looks like this:
- Formwork is assembled in the place indicated by the project.
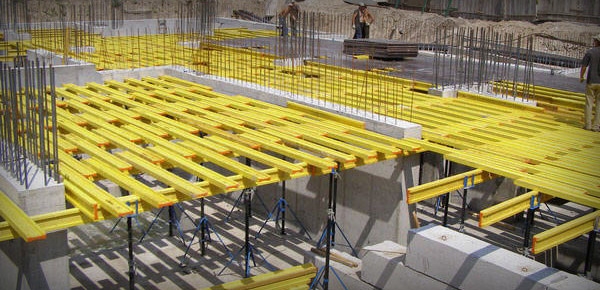
Assembly of formwork for floor slabs
- A reinforcing cage is mounted in the finished "bed".
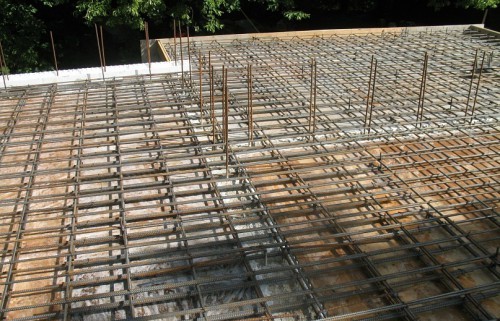
Reinforcing cage for a monolithic floor slab
– The last step is pouring concrete mixture onto the prepared area.
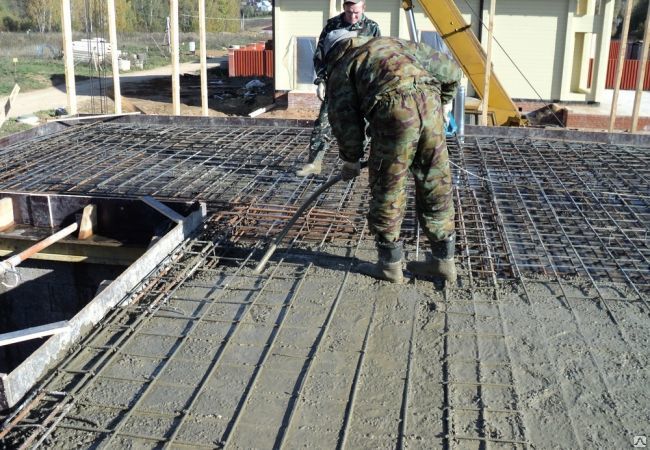
Filling formwork with concrete mix
Elements of prefabricated reinforced concrete are cast at factories of reinforced concrete products in compliance with all norms and standards. They are delivered to the facilities by special vehicles and immediately taken to work. Installation is carried out according to the design prescription.
Reinforced concrete slabs are categorized according to the criteria of internal structure and structural features. The classification includes:
1. Hollow-core slabs, marked "PC".
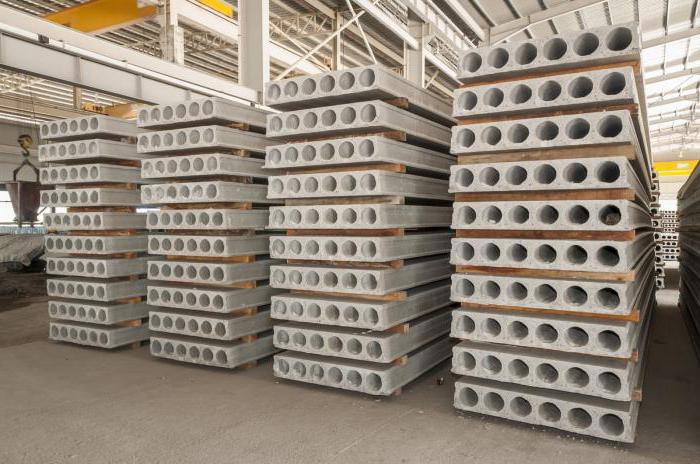
Hollow core slabs
2. Floor slabs marked "PPS".
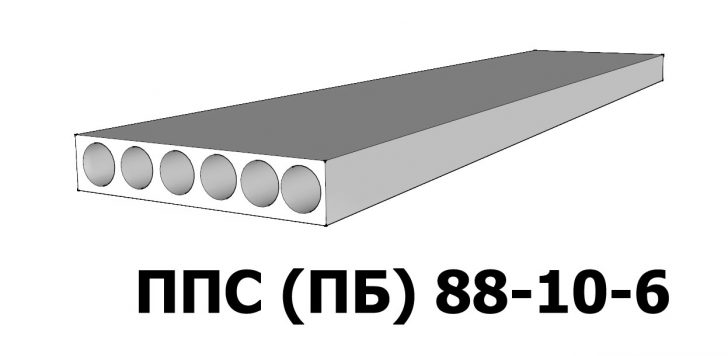
Floor slab PPS
3. Lightweight boards marked "PNO".
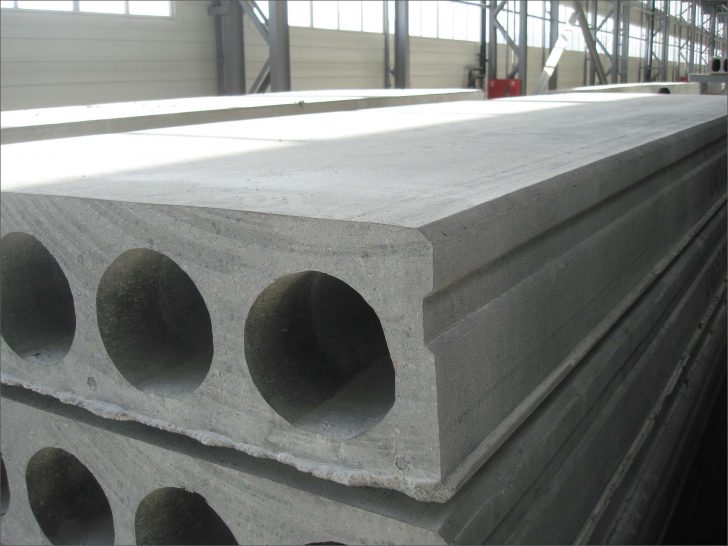
Floor slabs PNO
Solid boards
Full-bodied slab structures include:
1. Beamless.
2. Ribbed.
3. Caisson.
Beamless models
Plates of this type are monolithic, with a flat surface. They are supported by both walls and columns. These are representatives of exactly the category of reinforced concrete slabs that are recommended for the formation of floors in residential buildings.
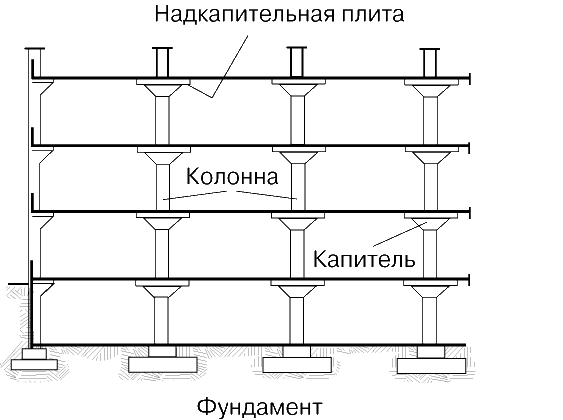
Beamless floor system
The smooth structure of the surfaces eliminates the need to hide the ceiling area behind the frames of suspended decorative systems during further decoration of the premises. The plate can be simply puttied and painted. Everything is simple and very beautiful.
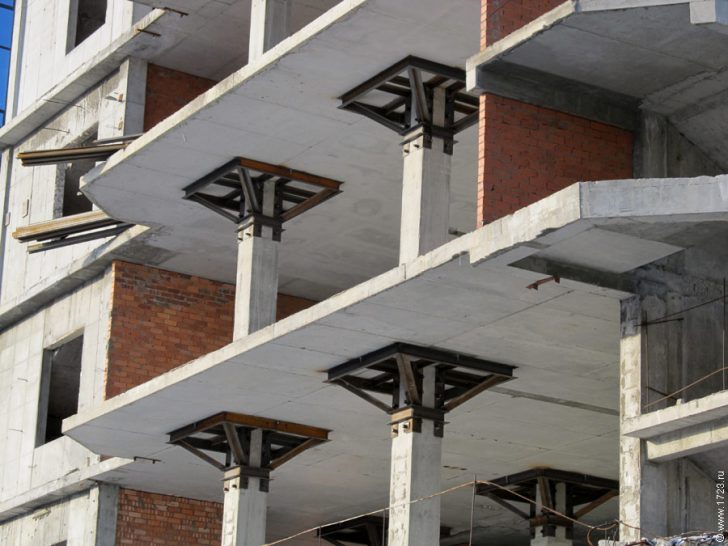
Beamless floor slabs
Ribbed models
Floor slabs of this series are a system, the skeletal component of which is crossed beams, with voids filled with concrete. Ribbed plates are ready to withstand the most severe loads. They are indispensable in the construction of large retail space and production halls where heavy equipment is installed.
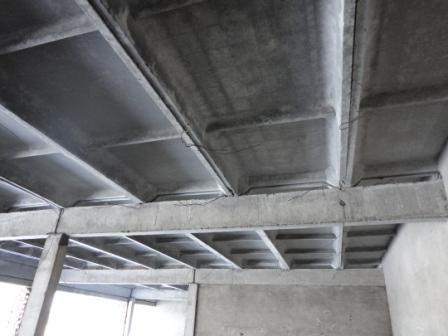
Ribbed floor slabs
For private construction of a ribbed floor slab, it is not advisable to use it for any reason. Firstly, it is expensive, and secondly, it is simply unnecessary.
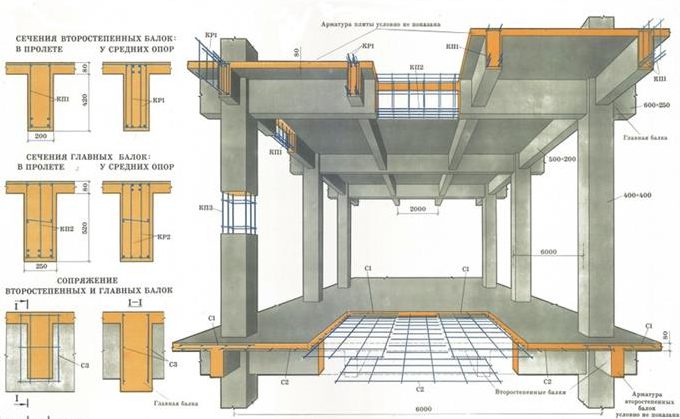
Caisson models
Their design is similar to the ribbed slabs described above, only a less thick layer of concrete mortar is poured into the cells of the grid formed by the beam base. This type of plate is also designed for the arrangement of industrial facilities and is extremely durable. For housing construction, it is not of particular interest.
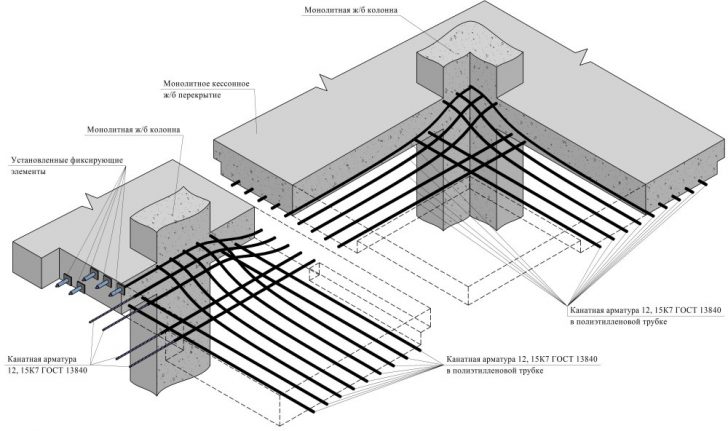
The essence of the coffered floor
What is good about full-bodied floor slabs is the unlimited size of their dimensions, since monolithic elements are assembled directly at their location.
Hollow-core slabs are cast in such a way that longitudinal gaps similar to the shape of pipes appear inside them. This reduces the total mass of the structure, creates additional stiffeners, and improves the sound absorption index.
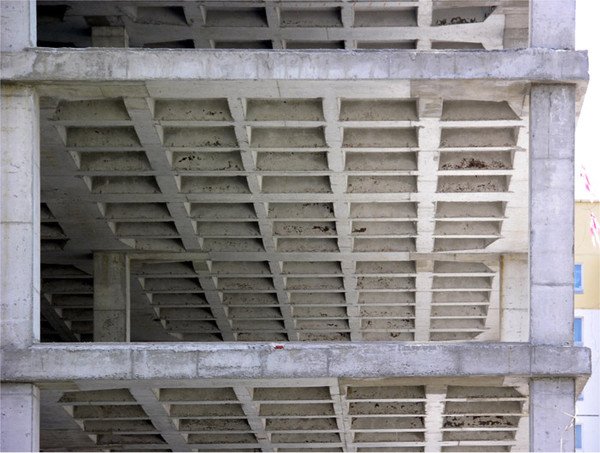
Caisson floors create additional stiffeners
Such an improvement allows the use of hollow-core slabs for covering large spans and in places of increased load.
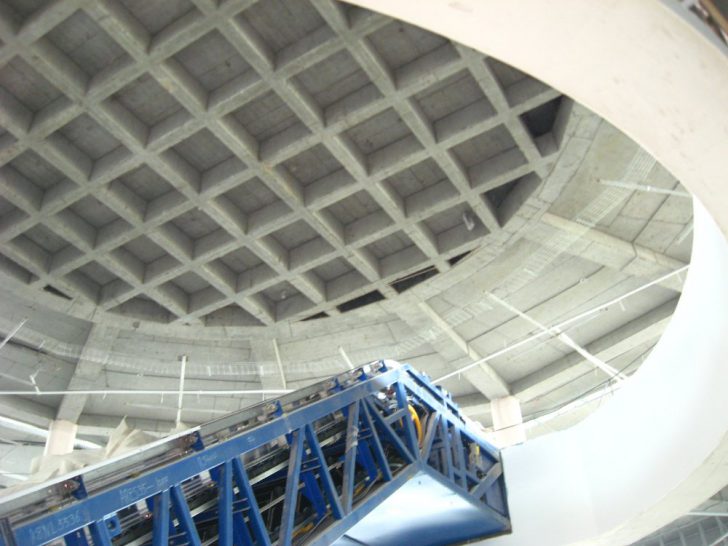
Caisson floor slabs
Plates of this category are distinguished by:
1. Form.
2. The diameter of the voids.
3. Overall dimensions.
In accordance with these features, hollow core slabs were divided into types, each of which received an individual marking.
- Products with rounded voids, 159 mm in diameter and 220 mm in cross section of the plate, are intended for covering walls supported on two sides. Their classification marking is 1PK.
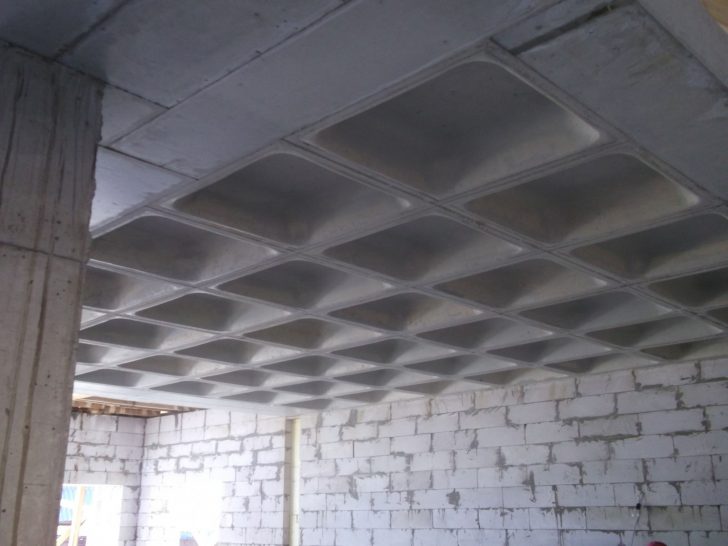
Caisson floor slabs with rounded cavities
- Reinforced concrete slabs with the same parameters of voids and slab section, but providing support on three sides, are marked as 1PKT.
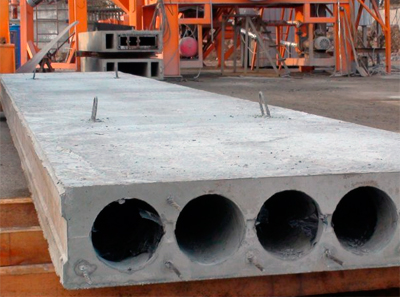
Floor slabs PKT
- Another representative of floor slabs, similar in all respects, requiring support from all four sides during its laying, was marked as 1PKK.
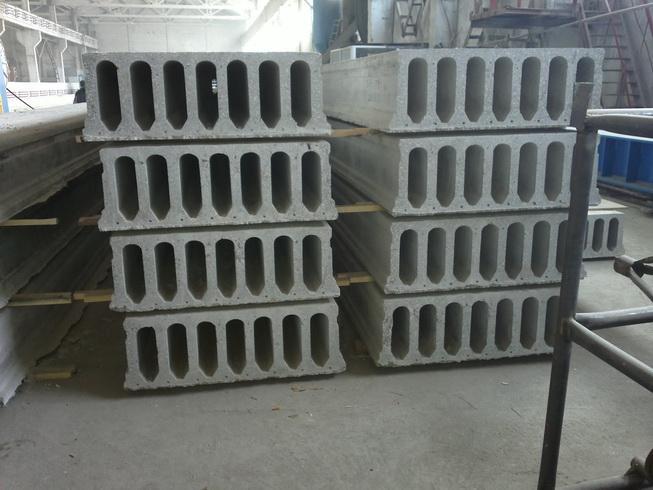
PKK floor slabs
- A 220 mm slab with a void diameter of 140 mm and laid with support on two sides was marked as 2PC.
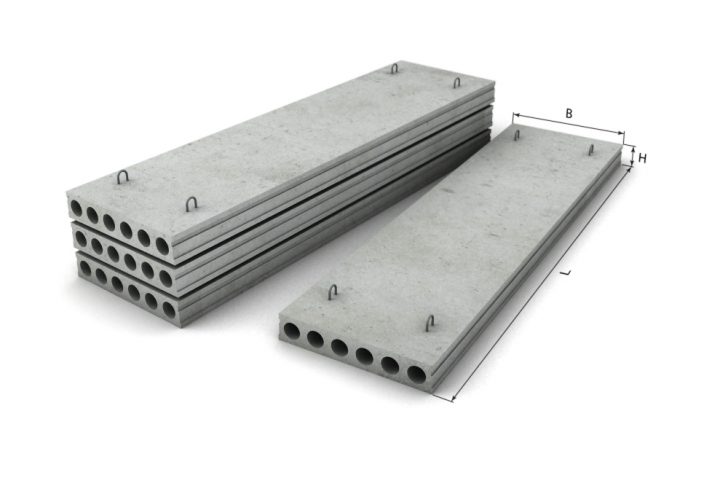
Floor slabs 2pcs
- Its analogue with three supporting sides, designated 2PKT.
- The last representative of this size series with a four-sided support is marked 2PKK.
– A hollow-core floor slab of the same 220 mm, but with holes, the diameter of which is reduced to 127 mm, with obligatory support on two sides of the end, is marked 3PK.
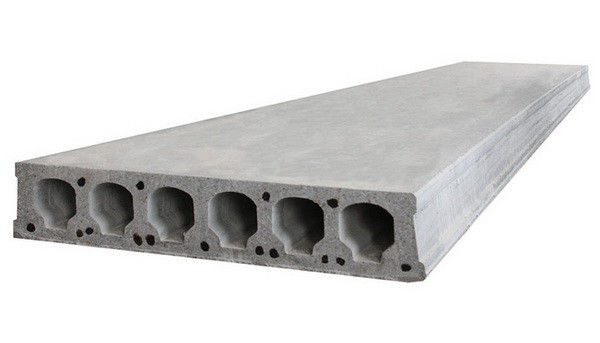
Hollow-core floor slab ZPK
- A dimensional analogue with three supporting sides is marked 3PKT.
- Accordingly, a slab with a size of 220 mm and voids of 127 mm in diameter, which needs supports under all four sides, is designated as 3PKK.
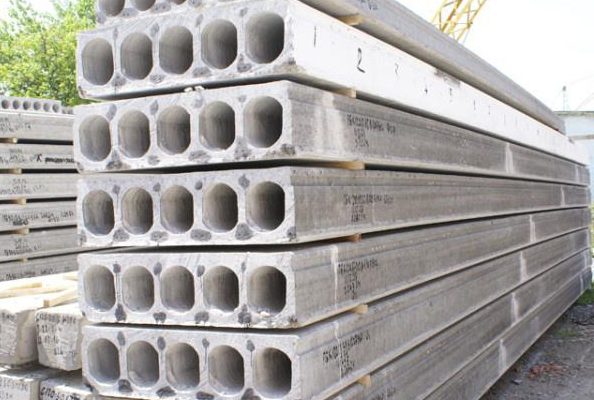
Hollow-core floor slab ZPKK
– 260 mm slab with 159 mm diameter rounded voids and two end supports marked as 4PC.
- A thicker plate, with a section of 260 mm and rounded gaps with a diameter of 180 mm, is marked 5PK. It has 2 end sides that support it.
- A two-support plate with a cross section of 300 mm and a hole diameter of 203 mm is designated 6PK.
- A reinforced concrete slab with a thickness of 160 mm and holes of 114 mm, also belongs to the subspecies of two-support models and is marked 7PK.
- A slab with a cross section of 260 mm and an oval shape of voids should rest on the walls with two ends. It is marked with the letters PG.
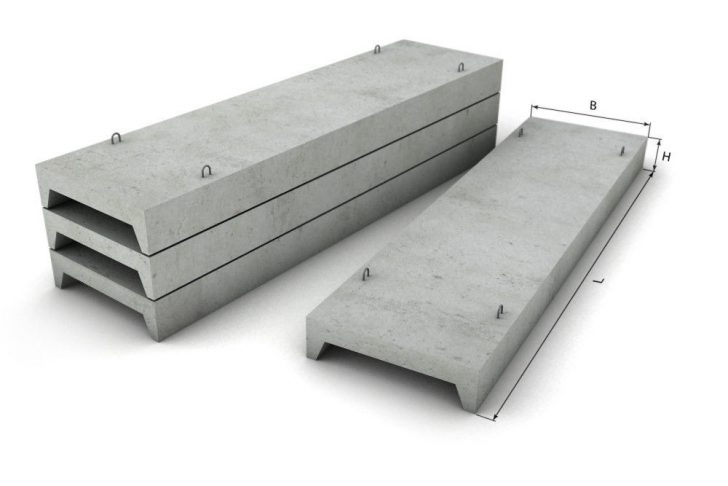
Ribbed floor slabs PG
– The last type of panel in the classification, produced by continuous molding.With a cross section of 260 millimeters and diametrical voids of 159 millimeters, they can be cut in the following unified sizes:
1. In length - 6 and 12 meters.
2. In width - 1. 1.2. 1.8 meters.
Support for such plates is needed under two end sides. The distinctive marking of the series is PB.
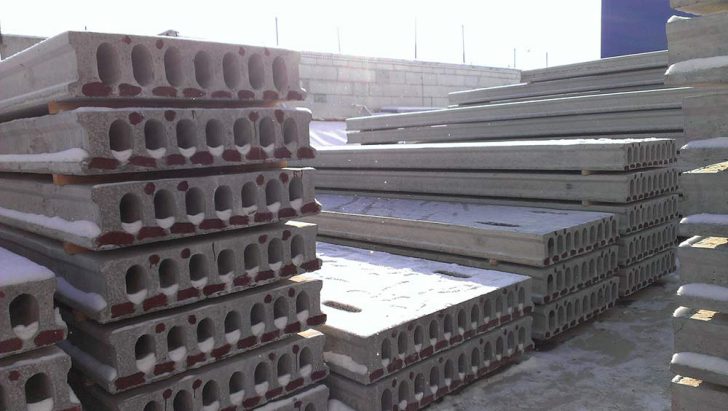
Formless floor slabs PB
In addition to the difference in thickness and geometric parameters, hollow core slabs differ in the way they are reinforced. According to GOST, products with two and three supporting sides are completed with prestressed reinforcement. A competent developer, seeing such slabs, knows that it is necessary to punch holes in them for laying communications in such a way as not to violate the integrity of the reinforcing mesh.
It is possible to break through floors of the PC and PG categories without hindrance. The diameter of their voids is at least 114 cm, which makes it possible to freely carry out sewage flows through them even with a cross section of 100 mm.
back to index ↑PPS slabs
These are products produced using a special stand, by longitudinal and transverse cutting. The stand resembles a hundred-meter-long rolling mill. The mixture of reinforced concrete moving along it goes through the stages provided for by the reinforced concrete manufacturing technology, after which it is sent under a diamond cutter for overall formation. This method of obtaining reinforced concrete slabs makes it possible to obtain floor structures of non-standard sizes and large lengths.
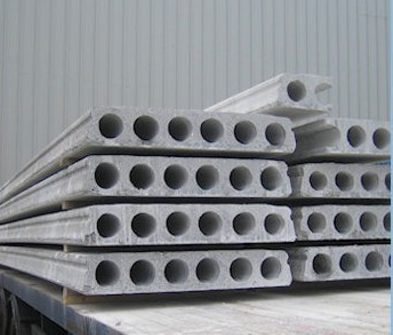
PPS floor slabs
Main technical parameters and decoding of markings
“Reinforced concrete floor slabs in the standard version have a thickness of 220 mm, however, there are also lightweight options with a cross section of 160 mm”
It is unnecessary to talk about the importance of a floor slab in building structures, therefore, the requirements of standardization during its release must be observed unquestioningly. Compliance with GOST should be manifested in everything, starting from overall indicators, but most importantly, the strength and rigidity of the product must comply with the requirements of the State Standard. Attention should be paid to resistance to cracking and some other parameters that are responsible for maintaining the design load.
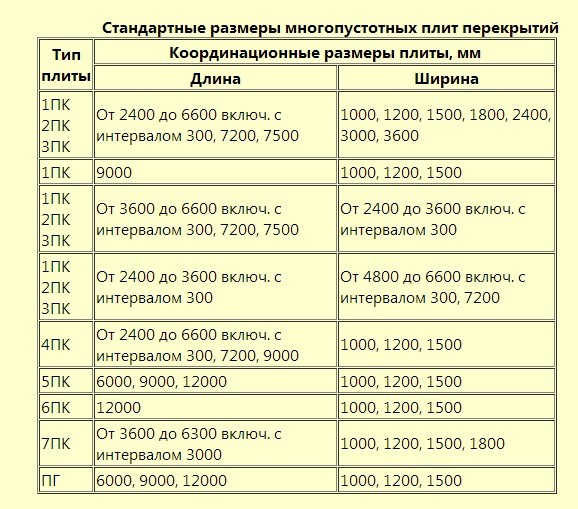
Marking and dimensions of floor slabs
According to GOST, all plates are marked in accordance with standard indicators. This is done for the convenience of designers and builders. The marking contains letters and numbers, the decoding of which is not difficult even for a non-professional.
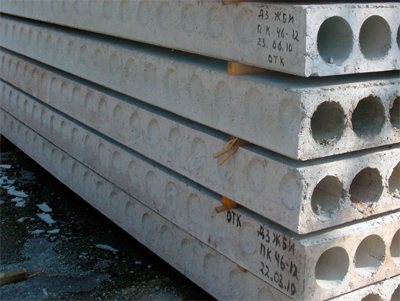
Example of marking floor slabs
The letters printed on the plate indicate the brand of the product. The two digits following them are the slab length indicator. It is encrypted in decimeters. The length is followed by the width. These are two more digits and the same decimeter scale. The last figure in the line expresses the indicator of the total design load, that is, the bearing capacity of the slab as a floor. The weight of the concrete itself is not included in this figure. The last letter at the end of the marking stamp carries information about the brand of concrete used.
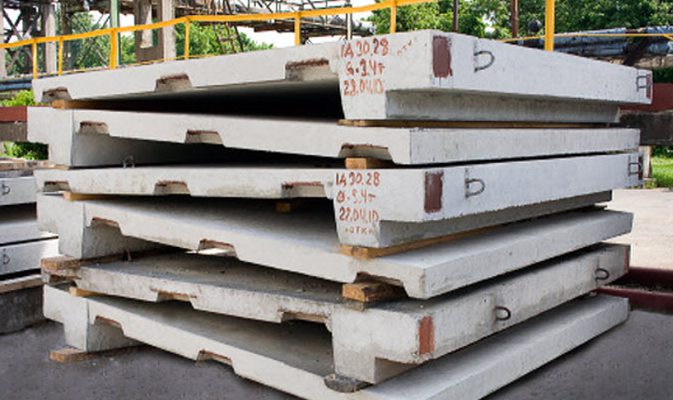
Marking stamp on the floor slab
Let's try to decipher the PC marking 60-12-9t. The letters tell us that the slab is round-hollow. In other words, the parallel holes forming voids in it are made in a cylindrical shape. The length of the product is 60 dm, the width is 12 dm, the maximum allowable load is 9 tons, and it is cast from M200 concrete mortar.
Reinforced concrete floor slabs in the standard version have a thickness of 220 mm, however, there are also lightweight options with a cross section of 160 mm. They belong to the third category of crack resistance, which indicates that the appearance of the latter on their surface is permissible during operation and the defect will not affect the main bearing indicators. There is a series of plates reinforced with additional reinforcement. Products from it belong to the class ATV. But still, the best bearing capacity is attributed to monolithic slabs.In the creation of floors of this class, reinforcement of the brand N is used.
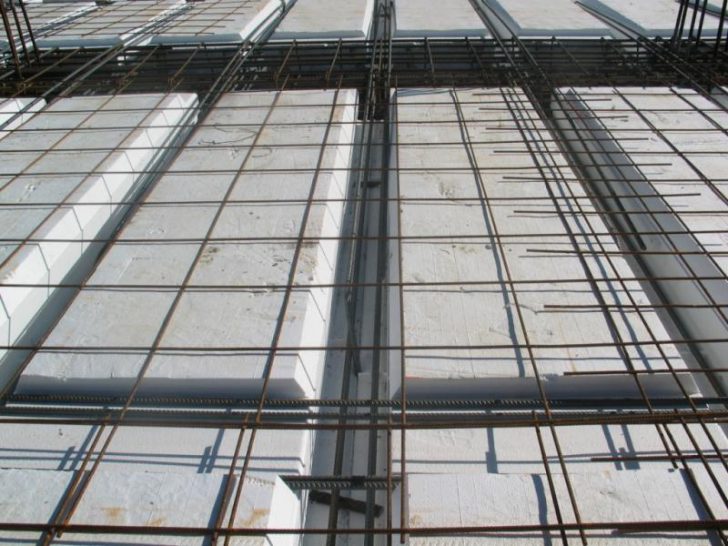
Reinforced concrete floor slabs
Comparative analysis of monolithic slabs and precast concrete slabs
Being engaged in the construction of your own house outside the city, you will certainly encounter the issue of purchasing floor slabs. What to give preference? With this, knowledge of the pros and cons of each type of reinforced concrete product will help you decide.
Let's start with monolithic views.
"For" them says:
1. Moderate material consumption.
2. No possibility of errors during installation.
3. No seams.
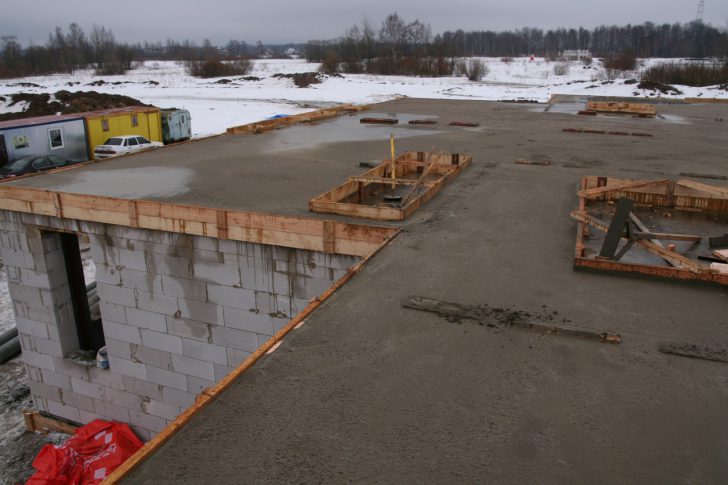
Monolithic floor slabs have no seams
4. Durability of the operational period.
"Against" testifies:
1. Seasonality of work.
2. The complexity of the process (the creation of formwork and expensive scaffolding).
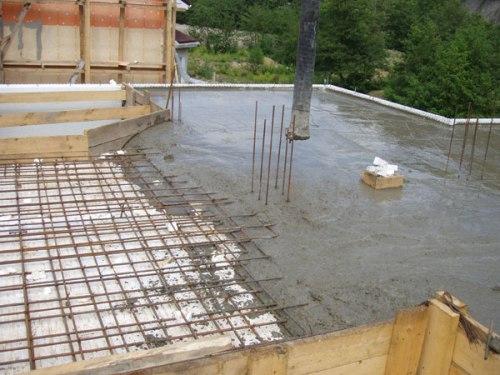
The construction of monolithic ceilings is a rather laborious process.
3. Delaying the construction time (you will have to wait for the concrete to harden naturally).
4. The need to attract specialists for the correct reinforcement of a monolithic slab.
5. The price of construction work with the arrangement of monolithic ceilings increases.
Advantages of factory structures of interfloor ceilings:
1. Production in workshops, in compliance with all technologies and laboratory quality control.
2. Easy to assemble.
3. The speed of installation work.
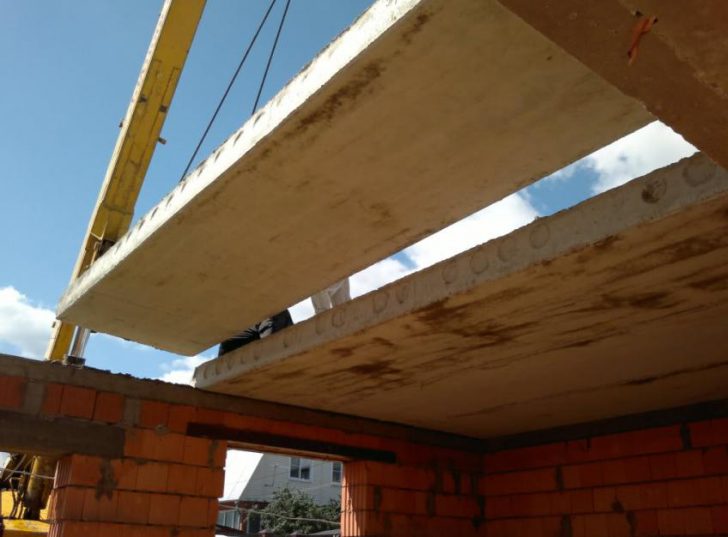
Factory floor slabs are quick to install
Of the shortcomings, one can note only a lower rigidity relative to the monolith.
back to index ↑How to buy floor slabs
When ordering reinforced concrete products, adhere to the following recommendations:
1. Send an application for the supply of concrete goods to the supplier in writing and be sure to wait for the invoice to be issued. Check it for a list of items, positional quantity of goods. This will eliminate misunderstandings during the actual receipt of the plates. The wrong size or the wrong quantity is fraught with additional delivery or exchange, which in the case of such bulky goods will cost a pretty penny.
2. Be sure to ask the seller for the name of the direct manufacturer of the material. You can go to his website and check reviews about the quality of products, see the reputation.
3. Pay attention to the grade of concrete used to cast the slabs and its quality.
4. Require the application of a quality passport for the goods supplied to you.

Quality certificate for floor slabs
5. Upon receiving the slabs, count their number and, without fail, inspect them externally for possible defects, such as cracks, chips, etc. If there are any, notify the supplier and draw up a defect report with the signatures of inspection witnesses. Perhaps in the future this paper will be very useful to you.
back to index ↑How to transport and store reinforced concrete slabs
“It is advisable to install floor slabs immediately after delivery to the construction site”
If the supplier is carrying the plates to you, then the responsibility for the integrity of the products will be fully assigned to him, but if you are self-pickup, then be vigilant yourself.
First of all, observe the rows of stacks in height, which is very important in the case of floor slabs.
Make sure that the plate rests on the bottom of the body with the entire surface, and not in parts.
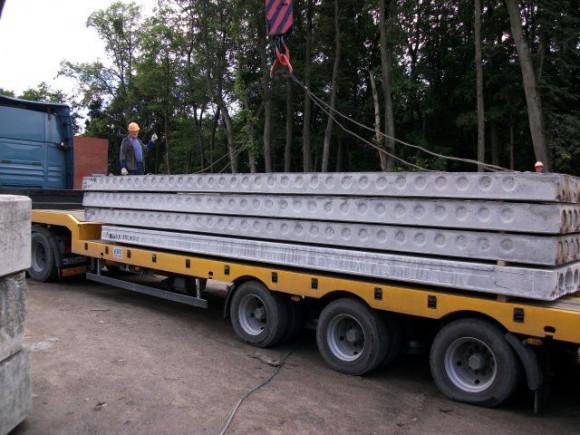
Transportation of floor slabs
Items cannot be loaded directly on top of each other. Use spacers made of wood. They must be laid so that they do not fall out during movement, that is, not under the very edges.
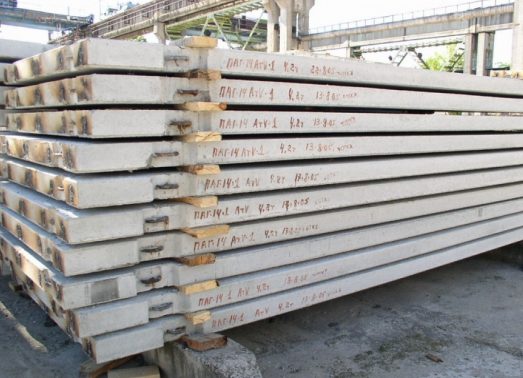
Cushioning bars for transporting floor slabs
As already mentioned, it is advisable to mount floor slabs immediately after delivery to the construction site. If this is not possible, you will have to organize their proper storage. To do this, do the following:
1. Select an area for storing boards corresponding to their length and level its surface.
2. Do not lay out reinforced concrete products directly on the ground.Ideally, scaffolding can be made from unnecessary pallets, which are usually always abundant at a construction site.
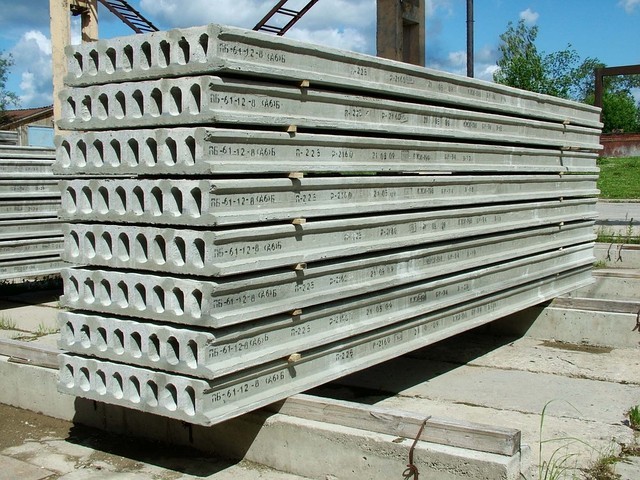
Floor slab storage
3. When unloading the slabs, as well as during transportation, lay them with wooden blocks, placing them 20 centimeters from the edges of the product.
4. Try to keep the vertical load uniform during stacking.
5. Arrange protection from precipitation. The easiest way is to close the plates with a thick film and tie them.
back to index ↑Conclusion
Previously, looking at reinforced concrete slabs stacked in piles, you did not even guess how much useful information their marking contains. All products were for you on one "face". But, faced with the direct process of construction, the gap in knowledge will have to be restored, otherwise you will not be able to fully control its progress.
Video